togwt
The Old Grey Whistle Test
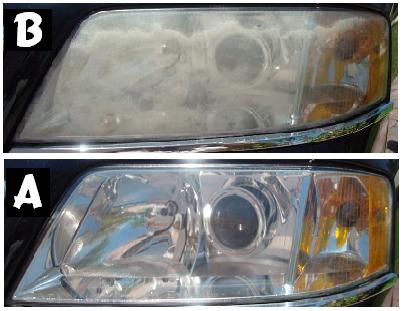
Headlight Restoration
Cause
Over the years, the polycarbonate headlight lens on any vehicle are subjected to heat and humidity - high Intensity discharge (HID) bulbs also bulbs also contribute to the deterioration of the polycarbonate lens as they emit heat from inside the lens, heat from the engine bay, radiation heat and humidity from the atmosphere, depending on climate and season Ultra violet (UV) radiation degradation causes oxidation and the lens becomes hazy and yellow. Road salt is also a yellowing agent, and then there is the effect of high-speed collision abrasion from dust, road grit and insects.
Effect
All of the above will cause the lens to become opaque causing lack of available road illumination. Hazy headlights aren’t just a cosmetic issue; they’re a safety issue, too and replacing headlights can get extremely expensive, and is often unnecessary.
Remedy
Because the damage on the lenses is usually purely superficial, they can be restored to an as-new clarity with minimum time and effort with the headlights still on the vehicle. If the lights are pitted, they will have to be sanded. But if they are just dull, hazy and yellow, surface polishing will restore clarity.
Lexan® Polycarbonate
In the late 1980’s, vehicle manufacturers changed the lighting lens system materials used for head lights from glass to a polycarbonate. Original equipment manufacturers (OEM) needed a material that could be moulded to aerodynamic shapes and was lightweight. A polymer material, Lexan® Polycarbonate, which was both lightweight and could be moulded into many different shapes aerodynamic shapes, making it suitable for sports cars.
Is a registered trademark of SABIC Innovative Plastics; a highly durable polycarbonate resin thermoplastic intended to replace traditional glass and Plexiglas where the need for strength and impact resistance justifies its higher cost.
Vehicle Head Lights
To the naked eye one cannot tell that these plastic lenses are actually a porous material that expands ever so slightly when it gets hot. Degradation of the lens occurs over time Having your headlights on or being exposed to the heat of the day causes expansion of the micro-the pores, allowing debris from the road to get in.
Headlights are usually made from Polycarbonate; it has its advantages (light weight, easily formed to differing aerodynamic shapes, etc) but also has its disadvantages; namely oxidation / discoloration or more correctly photo degradation
Tail light, turning and signal (turn indicators) are usually made from heat and impact resistant acrylonitrile butadiene styrene (ABS)
Oxidation (photo degradation) - of the polycarbonate headlight causes it to dry out the plastizers and become cloudy or take on a yellowish tinge. Ultraviolet (UV) rays from the sun also cause the lens to develop micro-cracks, hastening the colour change. If the lights are pitted, they will have to be sanded. But if they are just dull, hazy and yellow, surface polishing will restore clarity. This debris can be removed with a chemical paint cleaner (Klasse AIO or Werkstat Prime Strong)
Surface damage
When the lens starts to exhibit an opaque appearance and then a yellow hue on the outside of the lenses, this is due to ultra violet radiation (UV), which also causes micro-cracks. Road grit / debris and harsh chemicals cause surface scratches. This can severely restrict the amount of light reaching the road and this becomes a safety issue as you rely on the vehicles lighting system to see what’s on the road ahead and adjust your driving accordingly.
1. Tape-off all around the lenses so that you don't accidentally wet sand or buff the surrounding areas.
2. Using a random orbital buffer with a 3.5-inch backing plate and a 4-inch (Lake Country (LC) Mfg) White polishing pad or a terry cloth applicator
3. Place a small dab (about ½-inch diameter) of plastic polish on the foam pad or applicator.
4. Place the pad on the lens surface and turn on the machine (speed #4)
5. Polish the lens repeatedly in a left-to-right and an up and down pattern.
6. Continue polishing until all the polish is gone
7. Wipe the lens with a damp Microfiber towel
8. Inspect the lens; repeat the polishing process 2-3 times as necessary
9. Finally wipe down the headlight surfaces with isopropyl alcohol (IPA) or a tack rag to eliminate any residue.
Notes –
1. Polishing or wet-sanding will not remove clarity defects that are within the plastic but it will remove external/surface scratching and ultra violet (UV) oxidation (yellowing) as well as OEM applied UV protection that should be replaced
2. Softer polycarbonate resists breakage but will oxidize faster.
3. Don’t use abrasive or highly alkaline cleaners.
4. Never scrape the sheet with squeegees, razor blades or other sharp instruments.
5. Don’t clean Lexan® Polycarbonate products in the hot sun or at elevated temperatures as this can lead to staining?
Original equipment material (OEM) suppliers started to add ultra violet resistant (UV) coating to the surface of the lens in an attempt to reduce this condition and prolong the usable life of the lens. This protective coating is very thin (25 µ (microns or 1 Mil)
Removing oxidation or scratches from vehicle headlights or brake lights (also polycarbonate) also removes the OEM ultra violet protection, which prematurely decreases the durability of the lens. Surfaces that have yellowed are a sign that the ultra violet (UV) sacrificial coating has failed and must be resurfaced and recoated.
Ultra Violet Protection - polishing or wet-sanding headlights without renewing their ultra violet (UV) protection is a false economy, unless this protection is replaced, the end result is that you'll have to do them again in a few months (repeat this polishing process enough and there will be no material left to work with)
Preventive Measures
Preventive Measures
There’s nothing you can do to stop plastic from degrading, but you can certainly slow the process down, however, by avoiding salted roads and prolonged sun exposure whenever feasible. Cleaning the lenses on a regular basis (whenever you wash the vehicle) and using a mild , polycarbonate compatible polish on a semi-regular basis, and some companies even offer clear protective films that provide a buffer between your lenses and the elements. Such measures do more than just promote safety; they‘ll also improve the resale value.
In order to restore the lens back to its OEM standards a new ultraviolet (UV) resistant coating must be re-applied. For brand new vehicles, Optimum Opti-Lensâ„¢ will adhere to the factory-applied film to increase its life span. On refinished headlights, where the coating has failed and has been removed do to polishing.
Bonds directly to the polycarbonate finish due to its co-polymer resin content designed to bind with plastic and polycarbonate. Once applied to the headlight or other hard surfaces, the resin will form covalent bonds with the substrate and crosslink to form a permanent film. Opti-Lens coating contains high levels of UV blockers to prevent headlights from fading over time.
Apply directly to the headlight using a poly foam applicator or Optimum Dual Pro Applicator. Work a small amount of product over the lens using overlapping passes until it appears to melt into the lens and disappear. Remove any streaks or high spots with a soft microfiber towel. It takes approximately 30 minutes to cure before it can be exposed to water. Allow 24 hours to pass before washing or cleaning with pressure.
Alternate Product
G|Techniq C4 is a permanent headlight sealant; it has a durability of ~ two years (dependent upon conditions encountered).
Relevant Articles
1. “Environmental Damage� - http://www.autopia.org/forum/car-detailing/136393-environmental-damage.html#
2. “Nanotechnology coatings “- http://www.autopia.org/forum/autopia-detailing-wiki/136613-nanotechnology-coating-products.html
3. “Oxidation or Clear Coat Failure?� - http://www.autopia.org/forum/autopia-detailing-wiki/141208-oxidation-clear-coat-failure.html